Advertisement
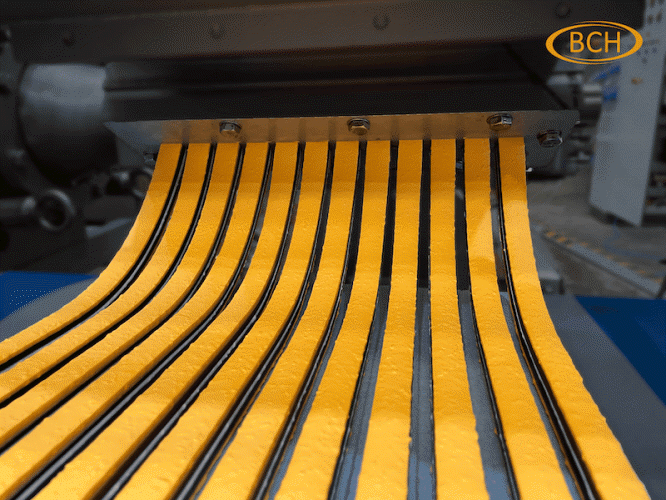
BCH’S confectionery extruders are primarily designed to handle liquorice and starch gels, but can also be used for fruit twists and sugar paste. These extruders are manufactured in stainless steel to a hygienic and robust design and in line with customer requirements.
Incorporating a BCH extruder into your production capacities allows for equal weight control, limited contamination of different colours and flavours, as well as providing a wide variety of shapes, centres and flavours/colours in liquorice products.
The extruder range can also be expanded after initial investment to include more options for liquorice production.
Twin Screw Extruder
The BCH Twin Screw Extruder is designed to receive continuously cooked liquorice feed from extrusion at higher pressures.
A vacuum point is included for precise product final moisture control.
Continuous / Batch Fed Extruders
Used in liquorice production, this extruder allows liquorice to be received directly from the Viscotator due to a small vacuum inlet hopper. This allows for the extrusion of a cooler, drier and firmer product.
Fitting a large feed hopper will allow for batch fed extrusion.
Side Flow Single Screw Extruder
Typically used for centre fillings / co extrusion applications or for the extrusion of batch cooked liquorice.
Multi Colour / Multi Flavour Extrusion
The BCH Multi Colour Multi Flavour extrusion line is now capable of providing up to 6 individual colours and flavours into a liquorice product.
The process begins with a neutral cooked product being fed into the BCH Twin Screw Extruder. The product can then be split into 6 individual channels and can be individually coloured and flavoured.
This method provides an automatic flow control of each colour channel to each rope of liquorice, eliminating the need for manual regulation of the machine.
Benefits of choosing a BCH Extruder
- Cost-effective
- High-output
- Quick start-up times
- Labour saving
- Unique CIP System reducing energy costs
- Precise continuous pressure
Incorporating a BCH extruder into your production capacities allows for equal weight control, limited contamination of different colours and flavours, as well as providing a wide variety of shapes, centres and flavours/colours in liquorice products.
The extruder range can also be expanded after initial investment to include more options for liquorice production.
Twin Screw Extruder
The BCH Twin Screw Extruder is designed to receive continuously cooked liquorice feed from extrusion at higher pressures.
A vacuum point is included for precise product final moisture control.
Continuous / Batch Fed Extruders
Used in liquorice production, this extruder allows liquorice to be received directly from the Viscotator due to a small vacuum inlet hopper. This allows for the extrusion of a cooler, drier and firmer product.
Fitting a large feed hopper will allow for batch fed extrusion.
Side Flow Single Screw Extruder
Typically used for centre fillings / co extrusion applications or for the extrusion of batch cooked liquorice.
Multi Colour / Multi Flavour Extrusion
The BCH Multi Colour Multi Flavour extrusion line is now capable of providing up to 6 individual colours and flavours into a liquorice product.
The process begins with a neutral cooked product being fed into the BCH Twin Screw Extruder. The product can then be split into 6 individual channels and can be individually coloured and flavoured.
This method provides an automatic flow control of each colour channel to each rope of liquorice, eliminating the need for manual regulation of the machine.
Benefits of choosing a BCH Extruder
- Cost-effective
- High-output
- Quick start-up times
- Labour saving
- Unique CIP System reducing energy costs
- Precise continuous pressure
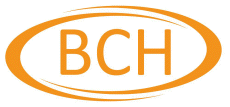
Millfold
ROCHDALE OL12 8DN
United Kingdom
ROCHDALE OL12 8DN
United Kingdom
more information
Hall 10.1 | A038 B039